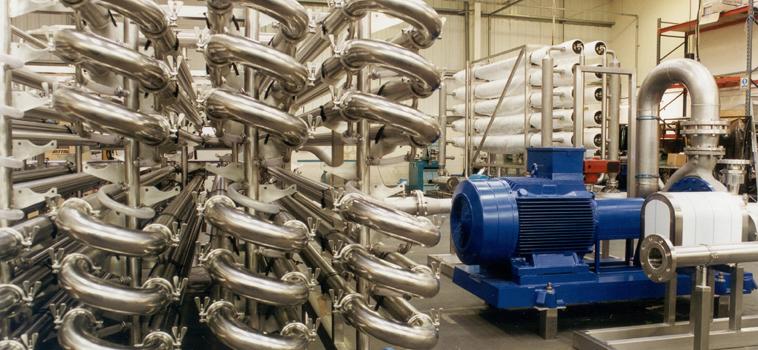
Industry Effluent
Industry Effluent
Chemical processors today are faced with mounting pressure to reduce wastewater volumes and treatment costs. While environmental regulations and “green” politics create a demand for companies to cut effluent volumes, economics also plays a major role. Discharge costs for wastewater are rising, as are charges for disposal and landfill of sludge generated from traditional wastewater treatment systems.
Fresh water prices continue to increase as demand increases and availability drops.
In addition, some effluent constituents, if recovered, can be quite valuable. For these reasons, discharging process wastewater can be literally like throwing money down the drain, especially when there are convenient alternatives.
One of the most effective approaches to dealing with some or all of these issues is crossflow membrane filtration technology. The technology can achieve a reduction in the volume of wastewater by a factor of typically 5-10 times and sometimes much higher. It offers potential savings on effluent charges, produces a stream of clean water, solvent or process fluid that can often be reused within the facility, and frequently yields retained waste material, uncontaminated by waste treatment chemicals, which can be reused in the production process or processed further to extract valuable raw materials.
Thus, it is often possible to achieve a true “closed-loop” or “zero discharge” plant. Payback on the capital cost of the membrane installation can be less than two years depending upon the application.
Key Applications:
- Recovery and reuse of water from waste streams
- Biomass separation
- Textile and dye effluent treatment
- Pulp and paper effluent treatment
- Landfill leachate concentration
- CIP solution recycle
- Pesticide and herbicide removal
- Food industry effluents
- Oily wastewater treatment
- Recovery of laundry water/detergent waste