Tomato Juice Concentration
BACKGROUND
ARP has expanded continuously since 1958 whe 7000 tonnes of tomatoes were processed, up to 100,000 tonnes/year (1984 figures). The factory produces 28º-30º Brix and 36º-38º Brix concentrate for major European clients.
PREVIOUS PROCESS
In the 1983 season the factory process was the standard hot break process with feed juice at an average of 4.5º Brix going to 2 large triple effect evaporators which concentrate 80 tonnes/hr of feed juice directly to concentrate/ paste product. The water removal requirement for 28º-30º Brix product was about 67 tonnes/ hr, with a steam consumption of about 25 tonnes/hr at an operating cost of £500/hr.
NEW PROCESS
ARP decided to expand production by approximately 50% over a two year period. Two competitive offers for a third large triple effect evaporator were considered in conjunction with PCI’s reverse osmosis system.
The traditional evaporator scheme would have required additional capital investment in steam boiler capacity, evaporator cooling system and the related civil engineering costs for these three major items. In addition to this, further increases in the already high fuel oil costs would make the evaporation step a major factor in the overall total processing costs for the factory.
1ST SEASON
The first stage of the expansion was carried out by installing the 42 tonnes/hr three stage PCI reverse osmosis plant. The line preconcentrated to 8.5º Brix, removing almost 20 tonnes of water per hour, with a total energy consumption of approximately 150kw of electrical power.
The existing evaporators carried out the final concentration to 28º-30º Brix or 36º-38º Brix. The initial expansion with the first reverse osmosis line increased overall plant capacity by 900 tonnes/day.
2ND SEASON
Two additional lines were ordered for 1985 to give a total reverse osmosis plant capacity of 126 tonnes/hr. All tomato pulp juice os preconcentrated to 8.5º Brix prior to the existing evaporators and the overall capacity of the factory was increased by nearly 50%.
THE SITUATION TODAY
ARP’s production has expanded to 150,000 tonnes of process tomatoes a year. New products have been added to their range such as cubed chopped tomatoes and concentrated tomato juice known as ‘Passata’.
The number of active farmers around Piacenza forming part of the co-operative has reduced slightly. However, they have embraced the new technologies allowing them to produce higher quality products with cost-effective production methods.
CONCLUSION
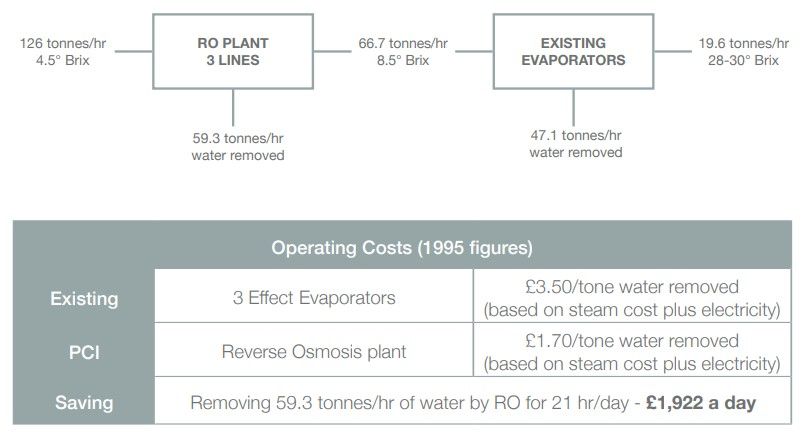
Customer Benefits
- Increase processing capacity by up to 50%
- Reduce operating costs by £1,992/day (1995 figures)
- Avoid costly investments in a new evaporator plus the associated new steam, boiler, cooling water system and services