MEMBRANE BIOREACTORS (MBR) SYSTEMS
Delivering higher effluent quality for a better tomorrow
By eliminating the need for secondary clarification and tertiary filtration, MBR technology is the market’s preferred choice for low to high strength effluents due to its proven ability to improve effluent quality and minimizing the treatment plant footprint. Moreover, this advanced process utilises a fully-automated process that minimized operators intervention.
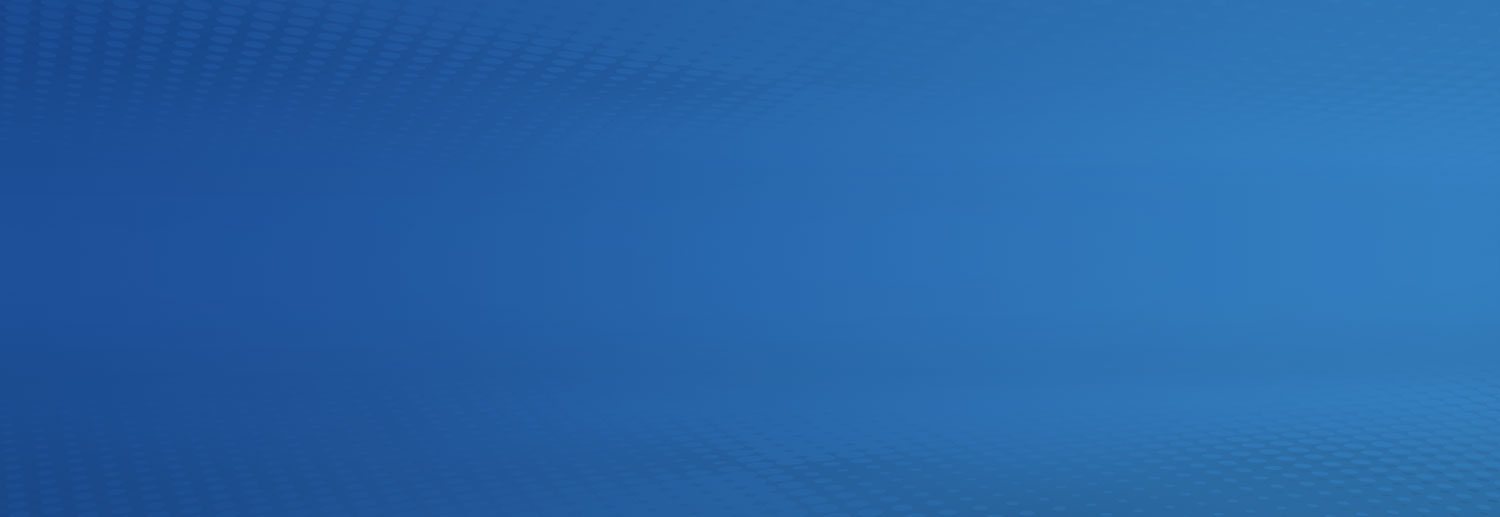
Our MBR solutions
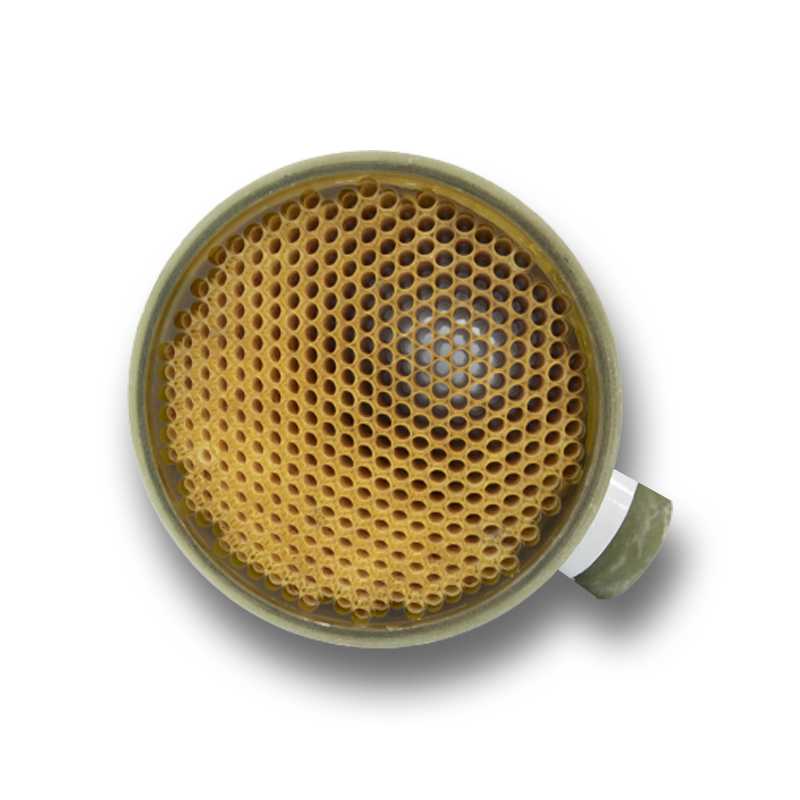
Our tubular module for side-stream MBRs: the A8 Series
PCI Membranes’ A8 Series is a tubular membrane module equipped with 8-mm tubes made of PVDF and 100 or 200 kDa MWCO (other selectivities are available at request). It has 8” (DN200) diameter and is 3 or 4 m long, with respectively 27 and 36 m2 of membrane area. The housing (module shroud) is made of GRP, thus having better chemical resistance to chlorine and strong acids as well as being lighter to handle than stainless steel solutions.
Thanks to its standardised design, A8 Series modules can be used for new installations as well as for replacing existing modules from other brands.
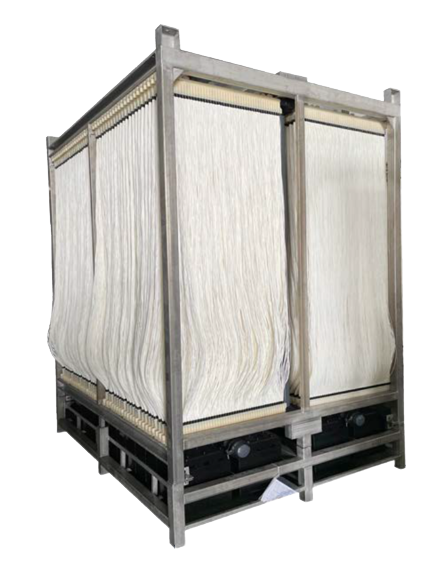
Our advanced hollow fibre cassette for submerged MBRs: the PCI-HF-Zmbr2 Series
PCI-HF-Zmbr2 Series is a hollow fibre membrane cassette equipped with backwashable PVDF membranes having a nominal pore size of 0.02 µm. Our hollow fibers are supported, enabling long, trouble-free operation before replacement.
PCI-HF cassettes are made of membrane modules installed within a stainless steel frame.
Zmbr2 modules are equipped with chambered fiber bundles designed to release air bursts to effectively scour the membrane surface while minimizing the required air consumption, thus minimizing the Operating Expenditure (OpEx). Moreover, their optimized hydraulic design enables minimum footprint requirements.
Z-mbr2 modules are available in 2 different heights:
• 2,142 mm (S-type), and
• 2,642 mm (U-type)
Where the latter is recommended if a deep enough membrane filtration tank is available as it allows to further reduce the specific scouring air demand.
As standard, two frame sizes exist:
• Up to 12 modules (that is, up to 480 m2 with S-type and 624 m2 with U-type modules), and
• Up to 40 modules (that is, up to 1,600 m2 with S-type and 2,080 m2 with U-type modules)
Tailored frame sizes are available on demand to minimise the footprint of your filtration tank as well as to replace existing cassettes from other brands.
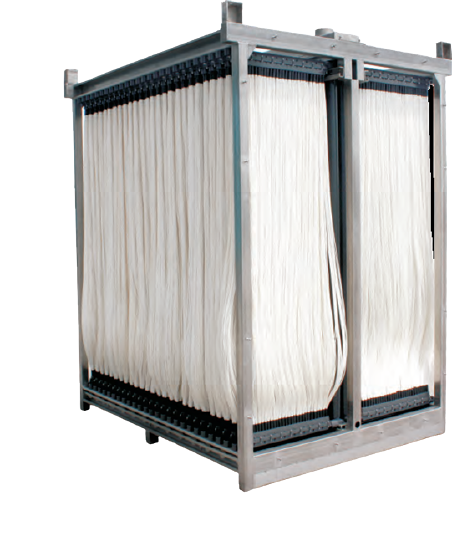
Our basic hollow fibre cassette for submerged MBRs: the PCI-HF-Gmbr Series
PCI-HF-Gmbr Series is a hollow fibre membrane cassette equipped with backwashable PVDF membranes having a nominal pore size of 0.02 µm. Our hollow fibers are supported, enabling long, trouble-free operation before replacement.
PCI-HF cassettes are made of membrane modules installed within a stainless steel frame.
Gmbr modules are equipped with perforated air pipes designed to effectively scour the membrane surface while minimising the Capital Expenditure (CapEx) associated with the membranes.
Gmbr modules are available in 3 different heights:
- 1,495 mm (E-type),
- 2,020 mm (S-type), and
- 2,520 mm (U-type)
Where the former is recommended for containerized and prefabricated systems while the latter is the recommended one if a deep enough membrane filtration tank is available as it allows to reduce the scouring air consumption.
As standard, three frame sizes exist:
- Up to 14 modules (that is, up to 192 m2 with E-type modules, 322 m2 with S-type modules and 434 m2 with U-type modules),
- Up to 26 modules (that is, up to 364 m2 with E-type modules, 598 m2 with S-type modules and 806 m2 with U-type modules), and
- Up to 52 modules (available for U-type modules only and offering up to 1,612 m2)
Tailored frame sizes are available on demand to minimise the footprint of your filtration tank as well as to replace existing cassettes from other brands.
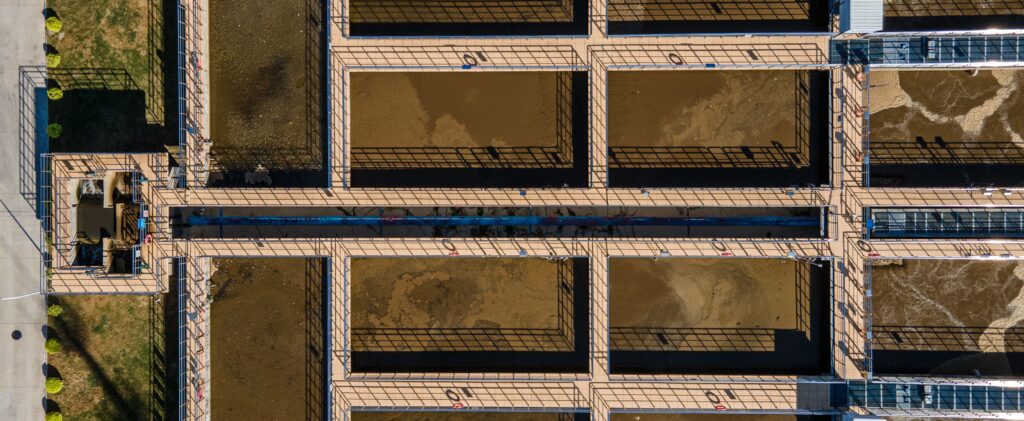
Which product is the right one for my application?
Have a look at our “Design of MBR Plants” article here to select the most appropriate MBR product for your specific application.
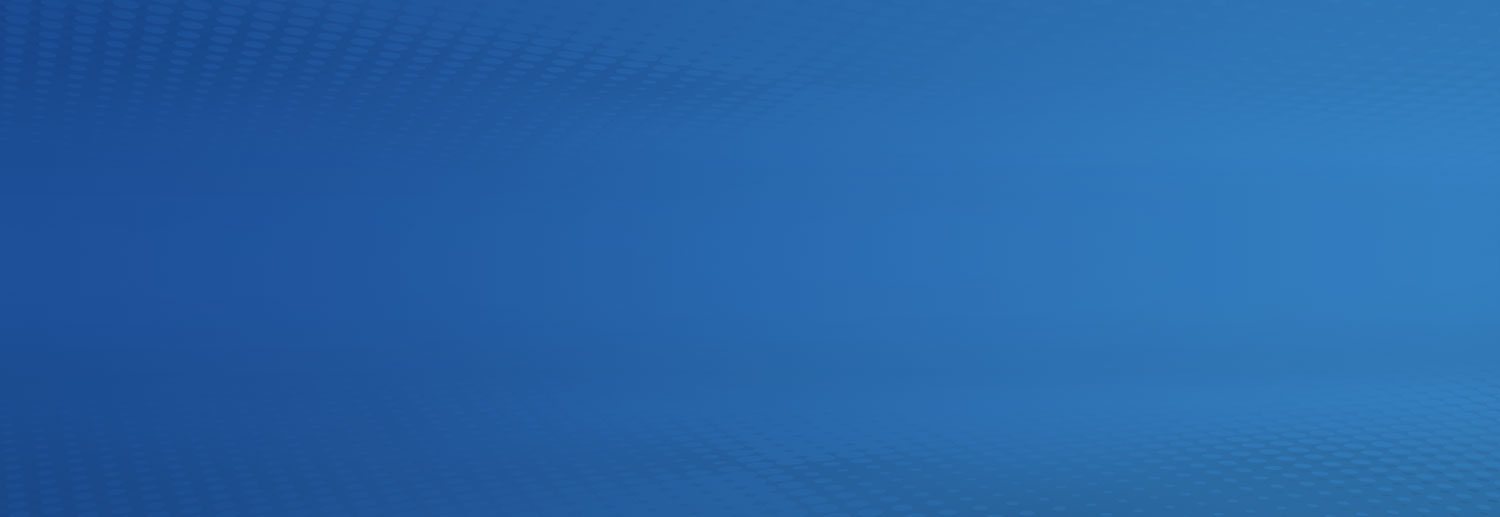
Advantages
✓ High effluent quality
When properly designed and operated, the MBR process easily allows the treated effluent to be discharged to sensitive receiving bodies or to be reclaimed for applications such as urban irrigation, utilities or toilet flushing. Meanwhile, the treated effluent is also of high quality for feeding directly to a nanofiltration (NF), a reverse osmosis (RO) or an advanced oxidation process (AOP) in case further pollutants removal is required.
✓ Smaller footprint
Large clarifiers no longer are needed. A smaller, often rectangular-shaped chamber, fitted with the membrane cassettes replaces the secondary settling tank whose size is governed by hydraulic and solids loading.
Because of the higher biomass concentrations that can be sustained within the bioreactors, the same total mass of solids is stored in a smaller tank, resulting in up to 60% smaller footprint for the whole biological and biomass separation process.
✓ Higher automation capabilities
The operation of MBR systems can be fully automated, minimising operators intervention that are typically required for conventional treatment plants. This means that the MBR process can be easily implemented also in decentralised and industrial sites.
✓ Modular design & tailored products
Our configurable MBR products fit to your site and perfectly satisfy your needs of today and tomorrow. Expanding MBR units using PCI Membranes’ products is quick and easy!
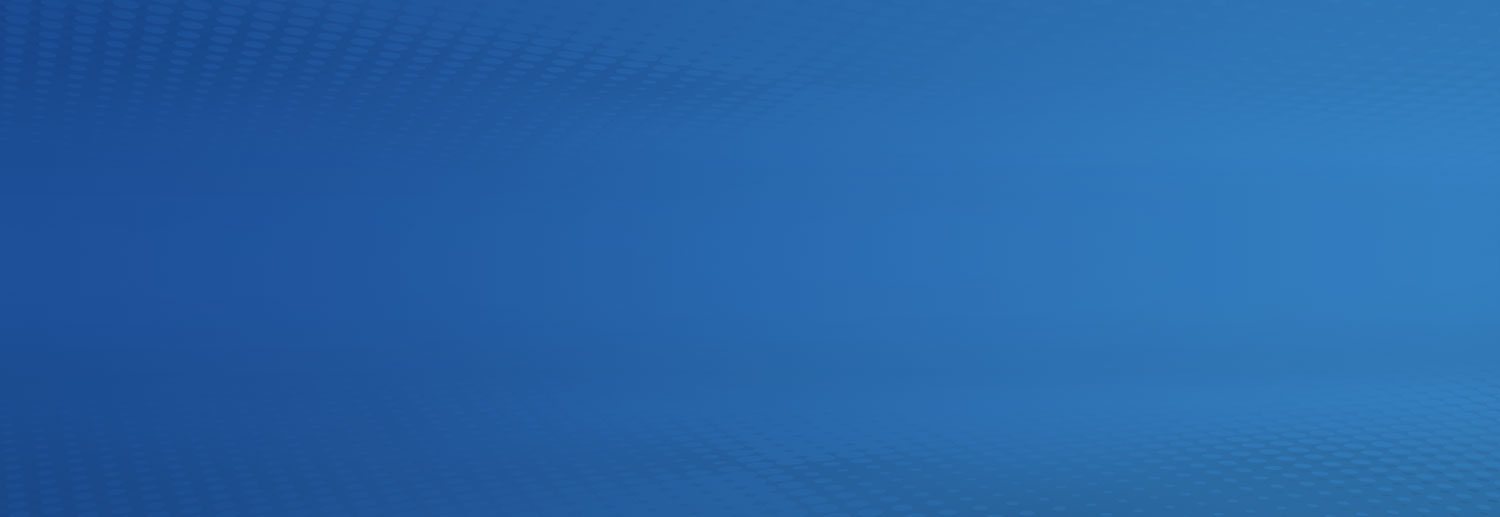
Applications
Municipal wastewater treatment
MBR systems were originally developed for municipal wastewater treatment applications, with a focus on water reuse and recycling. The MBR is an ideal process for treating or recycling municipal wastewater in water and space-limited locations because of its compact size, ability to produce reusable water (by retaining solids, bacteria and viruses), and trouble-free operation.
Industrial wastewater treatment
Industrial waste streams may include high organic loadings and chemical substances that are particularly difficult to handle or degrade, making biologically-stable processes like MBR more desirable. MBRs completely retain the biomass and this enables a higher biodiversity of the bacteria and protozoa population, favoring the biodegradation of recalcitrant substances (such as herbicides, pesticides, etc.).
Landfill leachate treatment
Landfill leachates usually contain high concentrations of organic and inorganic compounds. MBR systems have been successfully used in combination with additional treatment steps to remove soluble organics and for inorganics and heavy metals, such as nanofiltration and reverse osmosis processes.
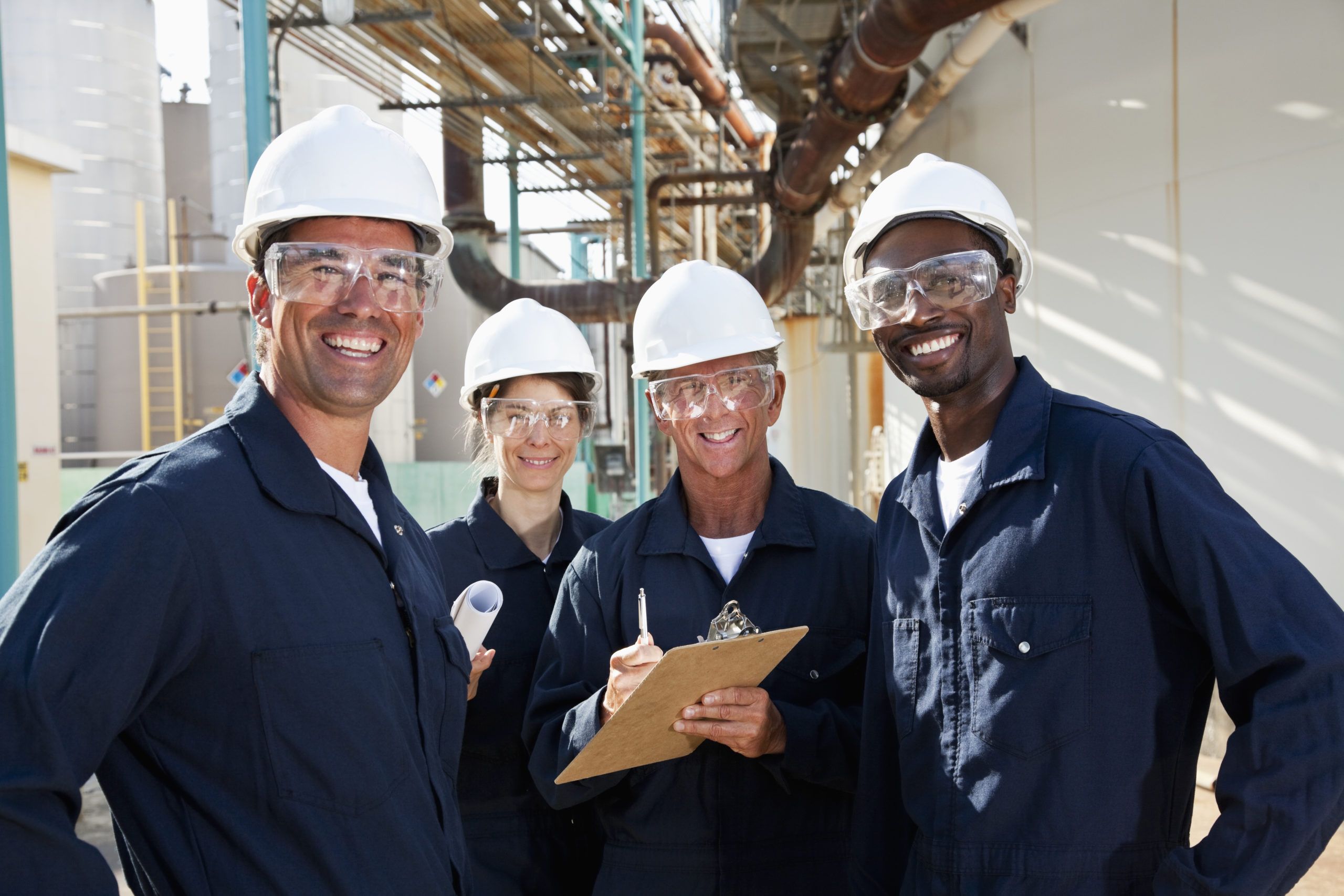
How can we help you?
Do not hesitate to contact our experts who will work with you to conduct project assessments,, customise, design and install your membrane filtration system, which best fits your needs.
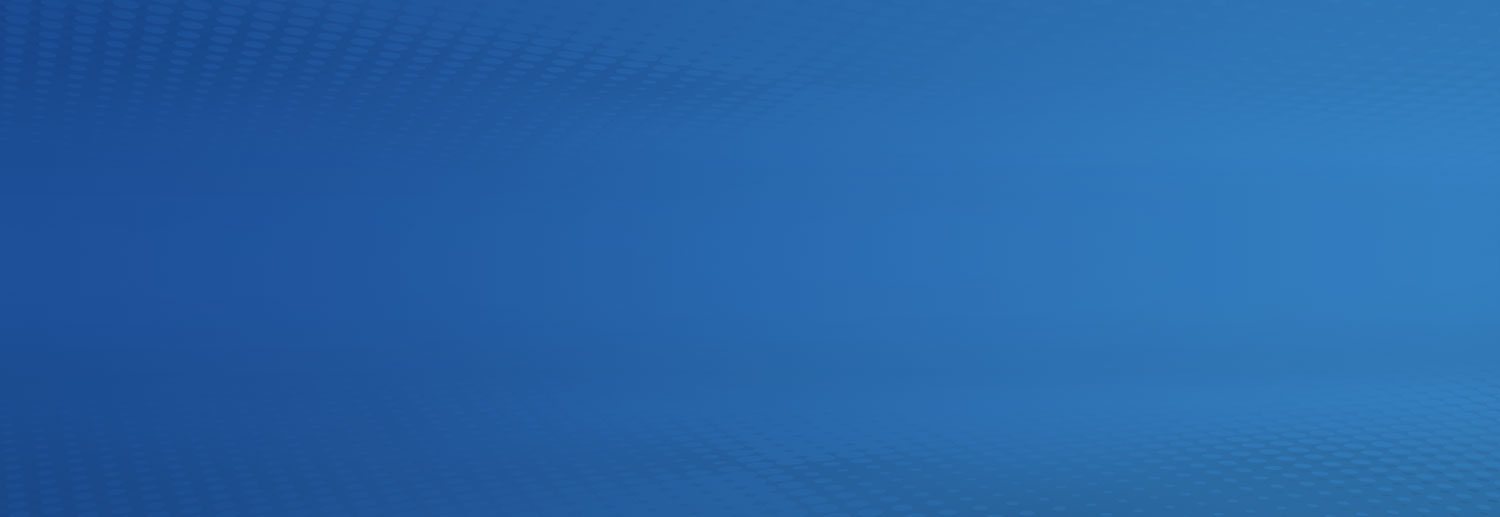
Learning Center
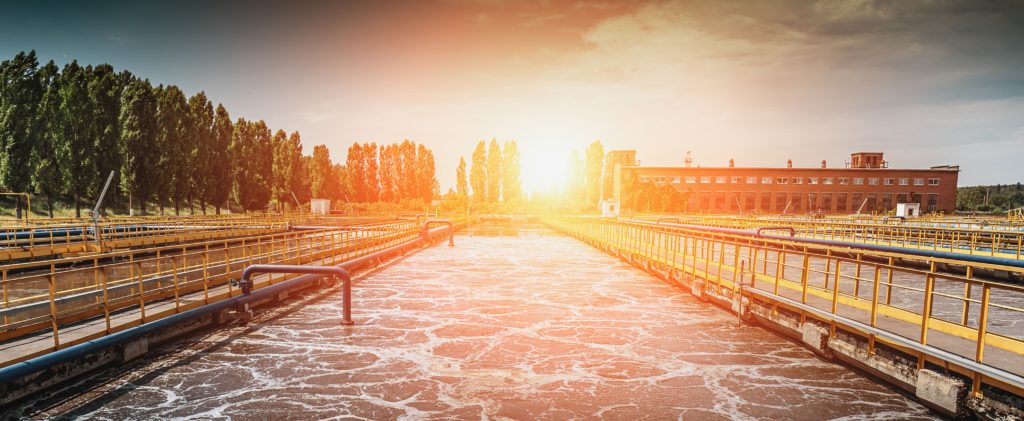
Membrane Bioreactors (MBR) for Wastewater Treatment
A Membrane BioReactor (MBR) is a process which combines a microfiltration or ultrafiltration membrane unit with a suspended growth bioreactor, and is now widely used in both municipal and industrial WasteWater Treatment Plants (WWTPs).
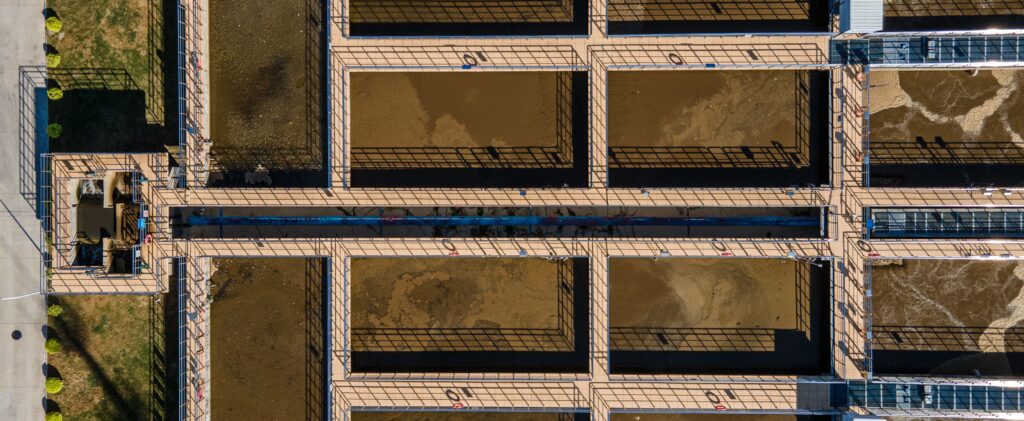
Design of MBR Plants
Learn how to design of MBR plants, advancing your wastewater treatment processes with improved performance and cost-effectiveness.
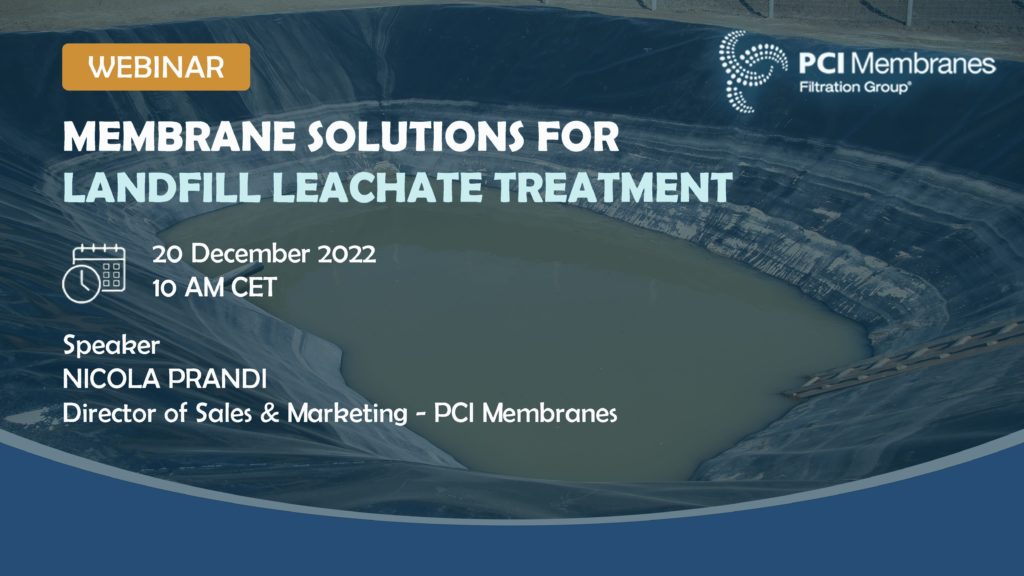
Webinar: Membrane Solutions for Landfill Leachate Treatment
Landfill leachate is known to be one of the most complex liquid wastes to be treated. Furthermore, it has to meet acceptable criteria to allow direct discharge into public sewage networks or natural water bodies.
Watch the “Membrane solutions for landfill leachate treatment” webinar replay to hear from our experts about different treatment techniques, and membrane solutions for landfill leachate.
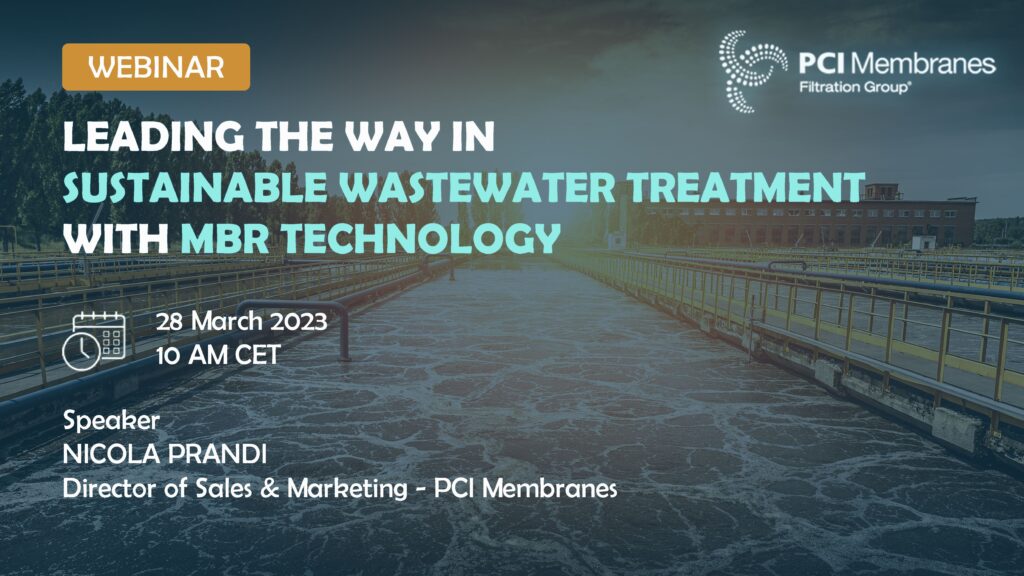
Webinar: Leading the way in sustainable wastewater treatment with MBR technology
Membrane Biological Reactor (MBR) technology is revolutionising the way we treat wastewater, combining biological processes with membrane filtration for efficient and sustainable results.
Watch the “Leading the Way in Sustainable Wastewater Treatment with MBR Technology” webinar to learn about the latest advancements in wastewater treatment and expand your knowledge on MBR technology!